“煤改气”致成本攀升,广东陶企如何降成本?
(来源:陶瓷信息网)2020年,陶瓷厂降成本的呼声越来越大。
“当毛利高达50%的时候,大家都不太在意成本的高低,当毛利只有5%之时,高企的成本会让企业举步维艰,甚至破产、倒闭。”一位业内人士分析到。
在广东产区,今年大规模“煤改气”致陶企生产成本普遍上涨2元/片;在其它产区,价格战“血拼”愈演愈烈,同样迫切需要降成本……可以说,陶瓷厂合理有效控制成本,关乎到企业的竞争力与生死存亡。
优化原料
降成本≠偷工减料
一位扎根陶瓷行业的业内资深人士告诉《陶瓷信息》,陶瓷厂降成本主要从两大方面着手:一是优化材料、提升工艺;二是改造升级设备,提产降耗。
具体来说,优化原料就是不断地寻找替代性材料。
该人士举例道,刚开始生产白坯成本不是很高,因为当时生产所用原料较为优质,直接使用就能达到白度要求。然而优质原料有限,后来就只能采用次一点的原料,此时需要增加添加剂,就是所谓的硅酸锆,当硅酸锆用量增加价格也开始上涨,后来就出现了复合锆。
“虽然目前陶瓷厂普遍能够接受复合锆的价格,但瓷砖价格又在走下坡路,为了进一步降低成本,又衍生出改进版的复合锆。”上述业内资深人士如是说道。
不管是优化原料,还是寻找替代性材料,都需要一个不断试验的过程。不同产区、不同陶瓷厂的配方体系不同,试验的结果也不尽相同,换而言之,就是充满不确定性。
不得不提的是,偷工减料≠降成本。富强集团副总经理梁汉培指出,“我们降成本需要坚持一个原则——不能为了降成本而降低产品的质量,警惕降成本演变成‘偷工减料’,坚决不能把砖做黑一点、釉料用少一点……”
“材料买得贵,却用得便宜。”梁汉培进一步说道,采购优质的生产材料,从表面上来看,材料单价虽然高了,但是在一定程度上而言,这与产品的优等率成正比关系。产品优等率高,配方成本就会被摊薄。
一位不愿具名的工厂人士透露,两年前,其工厂也曾一味地追求配方成本。当时工厂的配方成本可以做得很低,用高钙、高镁的高温配方,每吨粉料可以节省几元,每月的粉料用量大概是6万多吨。假如以每吨节省3元为计,一年下来大概可以节省近200万元。
但此配方也带来了很多问题,直接不良影响是:产量低,而且产品优等率低;间接影响是:失去了客户的信任,导致客户流失。总的来说,节省的不如损失大。
每个陶瓷厂都想方设法降成本,但是有些企业的老板就操之过急,用力过猛,只是给采购下硬指标——“不管你用什么办法,都要保证采购到最便宜的原料。”在此情况下,就很难保证产品的质量。
除原料优化外,降成本的有效方式还有工艺改进升级。据介绍,从低温慢烧到高温快烧的工艺改进,确实让陶瓷厂尝到不少甜头。以双零吸水率800×800mm规格产品为例,刚开始低温慢烧,要一个多小时。但现在,快则只需35分钟。
为配合高温快烧,粉料水分、压机压力、淋釉量及水分、窑前干燥等各环节都要相互配合。
设备改造升级
一次性投入大,效果立竿见影
众所周知,能耗成本、劳动成本在瓷砖总成本当中比重很大。而能耗成本又由多方面组成,其中包括球磨电力能耗,喷粉能耗,压机、釉线等传动电力能耗,窑炉燃料能耗等。“能耗成本至少占生产成本的30%,甚至有些陶瓷厂高达50%。”上述业内资深人士说道。
为了有效降低能耗成本,陶瓷厂会对设备进行技改、升级。“以往,对设备的技改很简单,就是单纯的加长、加宽,把产能拉大,把能源成本摊薄。”他进一步表示,未上宽体窑之前,只能过两片800×800mm规格的瓷砖,上宽体窑后,可以同时过3片800×800mm规格的瓷砖。“虽然一次性投入成本大,但是效果却是立竿见影。”
据悉,广东部分陶瓷厂在“煤改气”过程中,也对窑炉进行了技改,技改后单位气耗相差0.2~0.3立方米。
对于设备版块,在资金充裕的情况下,可以引进更先进的设备及技术。
据上述业内资深人士回忆称,2008年前后,当时有一家瓷片厂开年因招不到执砖工人而开始研发自动执砖机,虽然投入的科研、设备、调试、时间等成本相对较大,但当设备稳定运动、有效替代高昂的人工成本后,其效果凸显。
针对“煤改气”,在资金充裕的情况下,陶瓷厂将旧窑炉铲除,再建一条新的窑炉,确实可能节省不少的能源成本。现在有些窑炉公司也敢保证一定的能耗降低量,例如,原来单位平方米瓷砖使用1.8立方米天然气,新建窑炉后可能降低至1.5~1.6立方米。
内部管理
扁平化管理,向“潜规则”开刀
降成本是一个综合系统,除了材料、工艺、设备的优化、改造、升级外,还要注重对转产、库存等方面的管理及优化。
而且,发展至今,在陶瓷行业,回扣俨然已从“潜规则”成为了“明规则”。许多供应商为了推销自己的产品,常常采用不正当的竞争手段,用回扣等手段维护与工厂技术、采购人员的关系。
因而,供应链管理已经成为陶瓷企业降低成本的重要手段之一。佛山一陶瓷老板表示,当前陶瓷行业正面临着大洗牌,不断有陶瓷企业破产、倒闭的消息传出,严重影响了陶瓷厂与供应商之间的信任度。
信任度瓦解,致使陶瓷厂需要不断更换供应商,一方面不仅影响材料的稳定性,另一方面增加了很多采购的不确定性。
为有效地降低采购成本,很多陶瓷厂的老板直接管理采购版块,不仅采购效率高,而且采购成本也相对更低一些。
毫无疑问,想要长期降成本,肯定是现金采购为王道。
辩证看待煤改气
虽增加成本,但也提产5%~15%
近几年,全国各大产区纷纷掀起“煤改气”浪潮。今年更是蔓延至广东产区,广东的陶瓷厂纷纷进行“煤改气”。以天然气为主燃料后,陶瓷厂的能耗成本明显增长,增长的幅度大概是0.7元~2元/平方米。
据介绍,目前肇庆产区陶瓷厂使用的天然气热值并不稳定。当地一家陶瓷厂负责人告诉《陶瓷信息》,即便生产同一规格的产品,在产量及烧成时间等都没有改变的情况下,4条窑炉耗气量也存在差异。“有时候前后两天可以相差4000、5000立方米,使用天然气的成本波动还是挺大的。”
“在大概知道成本增长多少后,我们就不断思考如何通过其他方式抵消这部分成本,或是增加瓷砖的价值,或是在保证质量的前提下,综合其他方式降成本。”梁汉培如是说道。
值得一提的是,使用天然气之后,对产量的提升带来一定的积极作用。“我们工厂烧了两个月的天然气,暂时来说,产量确实比去年提高了。”梁汉培说。
不同产品的产量提升幅度不一样,大概在5~15个点之间。以800×800mm抛釉砖为例,使用天然气后,产量同比提升了7个点,“我们的目标是10个点,但要一步步来,毕竟有一个摸索的阶段,需要多方面的配合。”
陶瓷厂降成本的方式很多,不论如何都以稳为主,保证产品质量为前提,综合各环节以降低综合成本,切勿用力过猛,否则效果适得其反。
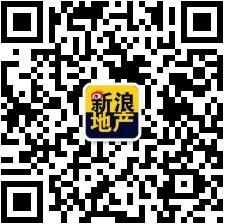