成本持续猛涨,对陶瓷产业链影响几何?
来源:陶瓷信息
已持续上涨近半年时间的瓷砖生产成本似乎仍未现“止涨”之势。近期来看,煤炭、钢材、化工原料等建陶行业生产“必需品”价格仍继续狂飙突进。“以一天一个价形容毫不为过。”有业内人士如是评价当前各类原材料成本上涨形势。
进入11月,“煤超疯”继续肆虐。国内港口方面,动力煤价格延续上涨,涨幅在14~32元/吨左右,主流成交价格(5500大卡)在691元/吨左右;环渤海动力煤(5500大卡)综合平均价格至607元/吨,环比上涨2.36%。
而在原材料方面,烧碱(在陶瓷行业主要用来生产水玻璃、减水剂)价格涨幅亦以“周”为计。11月份国内烧碱市场价格继续向好,山东地区32%烧碱上涨40元/吨;江苏地区32%烧碱继续上涨60元/吨左右;广东地区32%烧碱价格也有近100元/吨的上涨……
与此同时,2016已接近尾声,终端市场转淡趋势明显,生产成本的继续攀升对于挣扎在高成本边缘的陶企而言无异于雪上加霜,进一步加重陶企的经营和生存压力。并且,生产成本的上涨牵一发而动全身,深刻影响着整条产业链,对整个行业而言都为一次震荡。有业内人士认为,特别是在当前的产业发展背景下,将极大推动行业的洗牌化进程,留下来的企业在品牌实力、产品附加值、经营管理等方面的实力相对更为突出。
过去陶企利润很大部分源自生产成本下跌
近段时间以来,煤炭价格、物流价格上涨的消息不绝于耳,同时陶瓷化工原料、辅料价格基本上也全线上升,甚至是钢材价格也突然开始飙升,且仍在涨价中。在大环境整体形势低迷的情况下,成本的猛涨让下游陶企苦不堪言。
据本报记者调查了解,2016下半年以来,制造业原材料价格体系出现了重大变化,受国家供给侧结构性改革影响,大量行业产能遭到削减与控制,为制造业提供原材料的各种矿产资源价格一路上扬,直接导致了煤炭、钢材、化工原料等建陶行业生产“必需品”的价格不断上涨。
其中,涨幅最大的化工原料TDI在一年内上涨了5~6倍,从年初9800元/吨涨到现在的50000元/吨左右;炼焦煤主流品突破千元大关至1030-1100元/吨;氧化铝上涨幅度达到500~700元/吨;氧化锌上涨幅度达到了1000元/吨;氧化锆更是从26000元/吨涨到了28000元/吨,涨幅达到了2000元/吨……
原材料价格的全线猛涨,终结了“陶企生产成本持续下跌”的黄金时期。生产成本的瞬间猛增,引起众多重度依赖价格战的厂家的恐慌。
去年来,国内建陶行业持续低迷,大部分企业发展举步维艰,面临较大经营压力,但尽管如此,雪中送炭的是,2015年陶企综合生产成本大幅降低,原料、燃料、钢材甚至是纸箱等产品的采购价格大幅降低,综合来看,2015年陶企综合生产成本普遍下降7~15%。
此中利好,为陶企的价格战释放出较大空间。正因如此,自2015年来,部分产区价格战激烈程度空前,800×800mm规格抛光砖跌破11元/片,300×600mm规格瓷片跌破2.3元/片……产品价格达到历史最低值,并处于微利状态。
而到了2016年,陶瓷销售市场进一步转淡,生产成本持续下跌的红利却开始逐步丧失,随着近期煤价、物流运费及原辅材料的猛涨,一些一直处于微利,甚至是无利状态的陶企开始坐立不安,并开始蓄谋通过产品涨价来缓解经营压力。
山东淄博一陶企向记者表示,自8月下旬以来,淄博陶企用煤价格开始上行,由每吨480元的价格摇摇直上,在9月上旬达到700元之后,又分别于9月下旬涨至730元,10月中下旬涨至770元,10月底攀高至当前的840元。按照该公司一条生产线日用煤炭60吨、每吨上涨360元的涨幅计算,该公司一天就比8月份前多支出21600元的费用,一个月下来,将近多支出65万元。以其日产10000平方米瓷砖为例,仅煤炭一项,每平方米瓷砖的生产成本至少增加2元。
中国建筑卫生陶瓷协会常务副会长缪斌曾在公开场合表示,在“十三五”期间,陶瓷行业面临的挑战之一就是煤炭等原料价格及生产成本的上升。“过去很多陶企的利润源于原材料价格及生产成本的下降,而现在及未来这一红利将消失。”同时,“十三五”是建陶行业结构调整、转型升级的关键时期,在这个时期,去产能、去库存是首要任务,预计至少四分之一的产能在“十三五”要被淘汰,这也意味着一批建陶企业在“十三五”期间会出局。
色釉料:供应商称“临近亏损边缘”,酝酿集中提价
作为陶瓷釉料中占比最大的原材料之一,氧化锌自开启涨价模式以来,价格已经历经数度翻涨。据知情人士透露,至11月10日左右,在这一轮涨价中,业内的氧化锌价格已经上涨了1700元/吨,低品位氧化锌(85)涨幅甚至已经突破2400/吨。
“预计涨势还会持续。”某釉料公司负责人指出,受到环保因素及国际市场波动影响,有色金属涨势仍在持续,这也预示着氧化锌、氧化铝等与有色金属联动性较强的陶瓷化工用品价格仍在相当长一段时间内保持上涨姿态。
虽然价格并未上涨至历史最高位,但对于釉料企业来说,压力已经不容小觑。“这一轮涨价恰逢陶瓷终端市场萎靡,陶瓷企业销售不畅,因此对于采购价格控制极为严格。”上述负责人表示,鉴于目前的行业背景,即使原材料价格涨势凶猛,截至目前,多数化工、色釉料企业的涨价措施也难以实施。
“为了维系一些优质客户,公司甚至不得不给出更低的价格,如此一来,利润基本处于亏损边缘”。一位不愿具名的供应商代表透露,无力涨价的原因也包括目前色釉料企业仍有相当大的库存。他认为,这一轮原材料价格上涨,会对整个行业起到洗牌的作用。
该供应商代表告诉记者,在涨价期,除了原材料的源头供应商利润会有所增长之外,产业链下游的整体利润空间都会受到挤压。“从目前来看,此次涨价所带来的影响最终需要整个产业链一起去消化,包括瓷砖价格、化工釉料价格等都需要调整”。但他同时指出,即使如此,产业链的整体利润也依旧会被挤压,其中,化工、色釉料企业等中间环节受到的挤压是最严重的。
依照该人士分析,每一轮价格上涨,都会对化工、色釉料等中间环节的企业造成损失,甚至可以说是不可恢复的。“在上一轮有色金属、硅酸锆价格上涨期间,我们的利润最低时被压缩至原有的20%,虽然后来随着原材料价格的下调,利润有所回升,但是再也达不到之前的水平。”在他看来,这一轮涨价恰好碰到了瓷砖消费市场萎靡,陶瓷企业销售不畅致使化工、色釉料企业价格提振无力,若是持续发酵,影响将极有可能比上一轮更加严重。
“色釉料企业正在酝酿集中提价,但具体时间仍未确定。”知情人士向记者透露。
中间商:“原材料涨价,我们压力最大”
此轮原材料价格大涨,影响的不仅仅是陶企和原料生产商,对于中间商而言亦为较大的震动。
佛山某解胶剂中间商章先生告诉记者,近两个月来,片碱与液碱价格不断攀升,片碱价格与年初相比上涨了近2000元/吨,涨幅超76%。在此背景下,以片碱与液碱为生产原料的水玻璃、解胶产品、氧化铝、氧化镁、羧甲基纤维素钠(CMC)等陶瓷化工料价格不断上调。“但我们与合作陶企的调价并不顺利。” 章先生坦陈,尽管已经与陶企协商微调供应价格,但远不及原料生产厂家上浮的价格,这导致产品利润空间大幅缩小。
另一中间商吴先生也表示:“产品利润空间压缩很正常,即便是遭遇超低利润或无利润,我们也得扛着。”采访中,多位中间商一致表示,对于他们而言,在原料供应环节更多拼的是“关系”。虽然目前的产品不获利,但谁知道以后的情况呢?只要关系在,赚钱的机会就相随。而一旦与陶企关系出现裂痕,就会永远断裂。”这将严重影响中间商与陶企的深入合作。通常来看,中间商所经营的产品品类非常多元。
“实际上,在此次涨价潮下,中间商的处境最为煎熬。陶企都同意我们涨价,但是涨幅远不及原料生产厂家供货价格。”吴先生说,原料生产厂家将大部分成本上涨压力转嫁给了中间商。“在陶瓷原料厂家看来,作为中间商的我们不认品牌、只认价格,哪里性比价高就往哪走,因此在成本上涨的过程中,基本将上涨的成本全转嫁到我们身上。”
但任何事物都具有两面性。也有中间商认为,这未免不是一次机遇。代理羧甲基纤维素钠的罗女士说,就此可以淘汰一批综合实力不强的企业。“此前存在一批“小作坊”生产企业,但他们的生产管理成本低,质量相对没有保证,因此售价较低。”正因如此,这类厂家扰乱了正常的市场价格体系,如今正好是一个调整期。
罗女士向记者透露,近期其公司被陶瓷厂家频频催货,但厂家对提价事宜还未有最终定论,以致不敢贸然发货。罗女士认为,羧甲基纤维素钠涨价是最正常不过的事情。在2016年中,羧甲基纤维素钠的价格已经跌至谷底7000元左右/吨,与高峰期的14000元左右/吨相比,下调的幅度将近50%。更为重要的是,此次涨价绝非个例,而是全行业的大范围提价。在她看来,“并不担心因提价而丢失客户。”
受访者一致认为,经历了此次涨价潮,无论是陶瓷企业还是受涨价影响的原料企业,明年都会迎来洗牌。一些代加工的原料厂,资金链在此大环境下很容易断裂。中间商也如此,与原料厂是预付款合作,而与陶瓷厂合作则是赊账模式。
倒逼陶企进步
对于陶瓷企业而言,令其感到无奈的是,在原材采购端遭遇成本上涨的同时,出货产品价格却难以实现“上涨”,虽然此前江西高安、湖北、山西、辽宁等产区陶企为应对成本上涨压力,都曾商议“统一涨价”,但在执行过程中,却仅有少数企业执行。“当前市场环境已经转淡,企业库存压力普遍较大,如果上调出货产品价格,很可能会面临客户流失,进一步加剧库存压力。”
如10月份的江西高安产区,在统一涨价倡议下,按协议涨价的陶企却遭遇销量急剧下滑的尴尬,部分陶企销量甚至因此锐减30%以上。
特别是对于过度依赖价格的陶企,不得不面对利润空间与产品销量的艰难选择。在采访中,北方多家陶瓷企业表示,通过此番运输费用、原材料、煤炭价格的上涨,把陶瓷企业最后一点利润给挤掉了,瓷砖成本价几乎等于售价。
但是在产能过剩、市场低迷,陶瓷企业库存高居不下的形势下,涨价只是陶瓷企业的一厢情愿,事实上几乎没有落实。缩减的部分利润空间,只能企业自己承担,并且若原料价格持续上升,企业负担还将进一步加重。在几乎没有利润的情况下运营,陶瓷企业资金压力急剧增加,运营风险明显加大。
事实上,对于陶企而言,面对此番生产成本猛涨,也并非没有应对之策。记者注意到,在全国多个产区,陶企更注重新品的研发生产和提升技术水平,更注重生产的精细化管理和生存成本的管控。在采访中,一些企业提出,在生产成本支出增加的情况下,会进一步强化内部管理,减少行政成本、人力成本等方面的支出,以求缓解压力。
同时,原料采购要求更加严格。据供应商介绍,部分陶瓷企业为了减少成本,对原材料采购要求更为严格,一方面提升了对质量的要求,稍有不合格就会压价;另一方面,一些陶瓷企业为了降低成本,直接用现金采购原料,但是价格会压得更低,以此来降低成本。
“过去,陶企盈利过于容易,生产管理普遍较为粗放,而当前成本和经营压力上升,将倒逼陶企技术进步和管理变革。”有业内人士认为,从某种程度而言,这对产业发展有利。
不仅如此,陶企推新品的积极性也大大提高。在普通产品没有利润的情况下,一些陶瓷企业推出新品以求增加利润空间。有企业表示,普通产品价格透明,并且同行还会互相压价,而推出新品就可以把价格定得稍高一些,且价格竞争相对较小,可以保证一定的利润空间。
在成本上涨风暴下,品牌型企业所受影响则要小很多。广东恩平某陶企生产负责人向本报记者坦言,当前各类生产成本猛增,对于生产成本极度敏感的陶企而言,无疑是致命的打击。以煤炭价格为例,今年来增长了300元/吨,一条线每月的用煤量为2000吨, 一年按10个月的生产周期计算,每条线年生产成本将增加600万元,如果再算上环保投入、物流以及其它原料的上涨,每条线年生产成本保守计算将增加1000万元左右。
“广东陶企的品牌化运营较为成熟,品牌的特性是价格稳定,因此无论生产成本如何波动,广东企业的价格体系都相对较为稳定。”多位广东陶企销售负责人表示,广东企业的利润空间相对较大,并且在过去生产成本下降之时,产品价格也并未波动。因此,抗成本上升风险能力较强。
在众多行业人士看来,虽然成本上涨对陶瓷企业生存发展影响较大,但同时也让陶瓷产业链发展更加良性,特别是在当前的产能过剩背景下,洗牌更利于行业发展,并且在经营压力的倒逼下,企业对创新、管理、品牌等方面亦更加重视。
(本报记者 操儒冰 张园 张诗华 崔学锋)
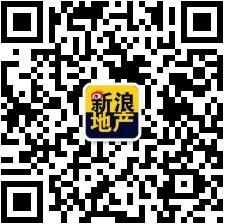